I know what you’re saying. “Wait, concrete? Like, in buildings? Not the rocky guy in the comcs, right?” And yes, I’m talking about concrete. More specifically, Portland cement – but since Portland cement is the primary ingredient of concrete, we’re really talking about the same thing.
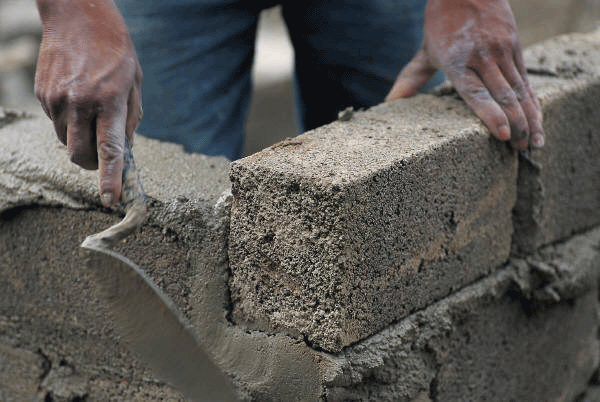
Every ton of cement that we manufacture produces .81 tons of carbon dioxide. Cement is made by pulverizing limestone under high heat, and when you do that, you produce CO2. Lots of it. Chalk in the CO2 cost of production and quarrying, and cement produces CO2 at one-for-one: one ton of cement, one ton of CO2. We the world produce 2.5 billion tons of cement a year. Cement, all by itself, produces five percent of the world’s CO2 emissions, and this is generally not well known because people focus their attention (understandably) on fossil fuel use. Hell, I follow global warming science much closer than average, and I didn’t know about it until a few weeks ago. To say that it blew my mind is an understatement.
Do we have alternatives to cement? Yes, there are options. Aircrete reduces the amount of cement needed to make concrete greatly by essentially treating concrete like bread (volume enhanced by air). High strength concrete mixes cement with silica fume or fly ash to make a block stronger than normal concrete by far, and with less cement by weight in the finished product. This guy, who apparently has multiple patents for medical cement, claims to have invented a cement manufacture process that doesn’t emit CO2 and in fact may even help to sequester it.
But Aircrete needs aluminum powder for its manufacture, and aluminum powder is horrible, global-warming-wise, to manufacture. High strength concrete depends on silica fume or fly ash, and one is mostly found in the Third World and the other you get by either pulverizing or burning coal. And the guy who invented eco-concrete is, as of yet, unproven. (But we can hope.)
Most of the reading I’ve done on the subject points to geopolymerous cement as being the best remaining hope for ecologically friendly concrete manufacture. G-cement doesn’t release CO2 into the atmosphere because it’s cooked at a lower temperature than limestone is, and we know it works because, well, it’s what the ancient Romans used. The drawback is that you still need some fly ash – but certainly not as much as you would find in high-strength concrete, where you’re using it as a binding agent in conjunction with regular old cement. Here, you’re using fly ash (or the right type of volcanic ash, if you can get it) as an ingredient in the cement itself, along with various sands. The fly ash is still problematic, but even with it, you’re losing vast amounts of CO2 production in the actual manufacture of the cement.
Of course, people have been discussing replacing traditional Portland cement with geopolymerous for more than a decade now, and nothing’s happened. Why? Simple: market economics. Geopolymerous cement is more expensive to manufacture than Portland cement. Admittedly, most of that additional expense comes from the fact that there’s no economics of scale at work, since nobody makes geopolymerous cement in mass quantities.
The answer here is frankly simple, although conservatives aren’t going to like it: the introduction of regulation. Carbon taxation and/or cap and trade might serve as incentives for cement manufacturers to diversify, but I personally prefer the stick to the carrot: allow a five-to-ten year timeframe, requiring production mandates for environmentally friendlier cement, and at the end of it, ban Portland cement. Period. The market is good, but it’s too slow; we need action, quickly, in this regard.
Related Articles
6 users responded in this post
This would be a good idea environmentally. But politically, it would set off a whine-o-storm. Increasing the cost of manufacturing houses in a down housing market would be like chucking moltov cocktails into a gas station during a fuel crisis.
In this case, I’m thinking a carrot would be better served than a stick. Offer tax breaks on houses that use G-cement and offer subsidies to companies that produce the product. With luck, that should have a reverse effect – making new houses cheaper to build and offering a new industry for entrepreneurs to invest in – which can give us a greener American jobs-friendly business.
Also worth questioning would be the insulation strength of various types of concrete. If Portland concrete offers a higher insulation strength than G-cement then, over a 10-30 year time frame, the energy you use to keep the inside of the building at the right temperature could outweigh the immediate benefits of the CO2 saved from more efficient manufacturing techniques. What’s more, insulation is generally always good, so if the insulation value of G-cement is better than Portland cement, that’s one extra selling point for the product.
Construction is not my strong suit by a long shot, but is there anything we could use INSTEAD of concrete, in any of it’s various questionable forms, as a substitute that would be better on all fronts, even marginally?
And to tag onto Zifnab’s comment about insulation characteristics, are the components for g-concrete much different from those of Portland concrete, and would the co2 emissions from the transportation of those materials to current manufacturing facilities have any impact on the total co2 output?
I don’t disagree with your suggestion of regulation, which I honestly think should be applied on a lot of fronts to jumpstart the needed progress which the market just isn’t stimulating. But from the little I’ve read on the subject, I think construction designs need to be re-evaluated on a lot of different levels to truly make a significant long-term difference. We’ve gotten stuck in a “traditional aesthetics” rut and don’t do enough to take advantage of the natural heating, cooling, insulation, stabilization, run-off, etc. opportunities in any given ecosystem.
This would be a good idea environmentally. But politically, it would set off a whine-o-storm.
I think the entire idea of these posts is that they’re good ideas environmentally and only not done because of political whine-o-storms.
And like MGK says, tax breaks are a great idea if you want industry to drag its heels for the next 30 years. Solar, anybody?
The first thing you’d need to do would be to duplicate the past 100 years of rigorous engineering tests regarding portland cement based concretes.
Then, you’d need to do a whole bunch more testing as to how it reacts with rebar, aggregate leeching, superplasticizers and other additives.
Now, we need to recalibrate every field testing unit in existence. What is the proper slump for g-concrete?
(Slump test is simply put, fill a warning cone with concrete, make a sand castle, and see how far down it “slumps” when the cone is removed. Except there is actually a standard cone to use.)
What’s the curing time? How much fresh water do we need to use during curing? Is the standard 28 day stress test sufficient to determine strength after pouring?
Then, you’d need to rewrite the entire Concrete Code.
I’m not saying it’s a bad idea, but these are the considerations that need to be made before we replace the single most important structural material in the world.
Cement produces 5% of the world’s CO2 emissions? Well holy shit. I completely understand where you’re coming from in terms of having your mind blown.
Your idea looks good, it must be said. However, I would use a carrot-and-stick method, and of course mightybaldking’s considerations are very important.
Now, do these figures reflect before or after the cement absorbs CO2? From what I understand, cement aborbs a bit over half the CO2 it produced when being made. Takes about ten years.
Also, China makes around a third of the worlds cement, so a big problem would be getting them involved over this.